Avoiding Common Mistakes in Construction Materials Testing
Construction materials testing is the backbone of any successful construction project. Whether you're building a residential structure, commercial property, or civil infrastructure, ensuring that materials meet quality and safety standards is critical to achieving durability and longevity. Yet, common mistakes in testing processes can compromise project outcomes, leading to delays, increased costs, or even unsafe structures.
At Terradyne, we’ve seen firsthand how careful adherence to testing protocols and industry best practices can make all the difference. In this guide, we’ll explore frequent errors in construction materials testing, their impact on projects, and actionable strategies to avoid them.
By following these insights, construction professionals can enhance safety, optimize project timelines, and ensure regulatory compliance.
Why Construction Materials Testing Is Necessary
Construction materials testing verifies whether materials such as concrete, asphalt, steel, and soil meet design specifications and engineering standards. This process ensures structural integrity, safety, and long-term performance. Improper or inadequate testing can jeopardize the entire project's success, costing valuable time and financial resources.
Still, despite its importance, many projects suffer setbacks due to mistakes in the testing process. Understanding where teams commonly go wrong is the first step toward improving outcomes.
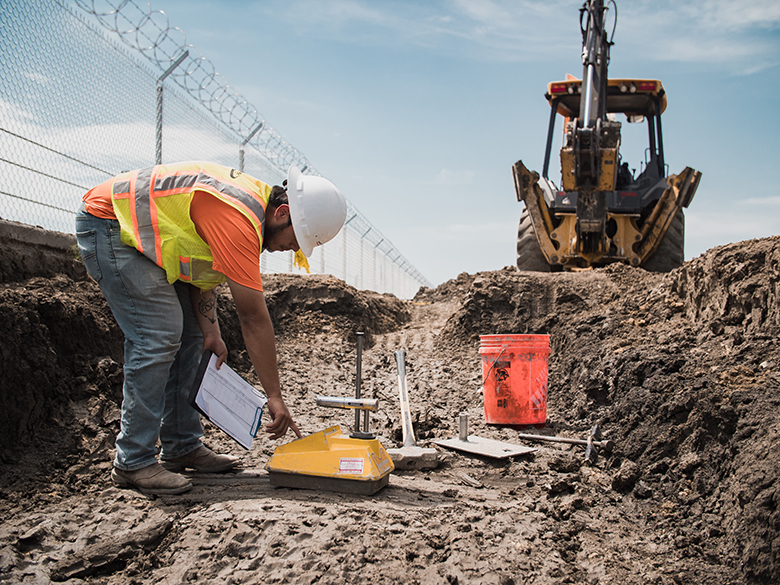
Common Mistakes in Construction Materials Testing
Even experienced professionals can make mistakes when testing materials. Here are some of the most common errors we’ve seen builders and engineers make, along with explanations of why they occur.
1. Inadequate Sample Collection
Materials testing begins with sample collection, and errors at this stage often compromise the accuracy of the results. Common issues include collecting samples that aren’t representative of the entire material batch or failing to preserve them properly during transport.
For instance, concrete samples may start to deteriorate if they are exposed to extreme temperatures before testing.
Why It Happens:
2. Improper Testing Procedures
Another widespread error is executing tests incorrectly. This can range from using outdated equipment to applying the wrong methods for specific materials.
For example, testing soil compaction with improper calibration can produce flawed results that misrepresent site conditions.
Why It Happens:
3. Lack of Documentation
Accurate record-keeping is often overlooked, especially during fast-paced projects. Missing or incomplete documentation can create legal and regulatory issues and hinder troubleshooting efforts when problems arise during construction.
Why It Happens:
The Impact of Mistakes in Materials Testing
Why do these mistakes matter so much? Because their consequences can ripple through every phase of a construction project.
Safety Hazards: Faulty or poorly tested materials can lead to structural failure, putting workers and occupants at risk. The stakes are simply too high to cut corners.
Project Delays: Mistakes can lead to repeat testing, casting doubt on timelines and pushing back project completion dates. This delay can spiral into broader disruptions for stakeholders.
Unnecessary Costs: Flawed testing often requires material replacement, redesign, or rework, increasing project expenses. Preventable mistakes like these can eat into your budget and reduce profitability.
Regulatory Penalties: Most construction projects are subject to rigorous compliance standards. Mistakes during testing can result in non-compliance, leading to fines, lawsuits, or project shutdowns.
Best Practices to Avoid Common Testing Mistakes
Implementing best practices for each stage of the testing process can help avoid mistakes. Here are some ways to ensure high standards in construction materials testing.
1. Master Proper Sample Collection
-
Always collect representative samples. This means pulling samples from different parts of the batch for concrete.
-
Use proper preservation techniques tailored to the material. For instance, soil samples should be kept sealed to prevent contamination.
-
Train your team in sample collection protocols to eliminate inconsistencies.
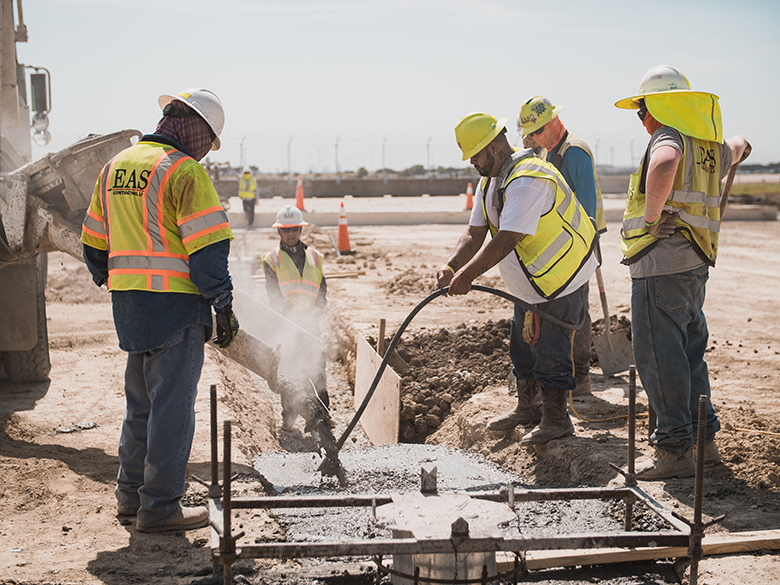
2. Standardize Testing Procedures
-
Update your testing equipment regularly to align with industry advancements.
-
To ensure compliance, reference the latest ASTM (American Society for Testing and Materials) standards.
-
Introduce periodic training programs for technicians to remain proficient in emerging tools and methodologies.
3. Implement Robust Documentation Protocols
-
Digital tools record every test, from sample origins to results. Cloud-based platforms can make data accessible in real time.
-
Standardize documentation formats across teams to avoid confusion.
-
Conduct regular audits to ensure your records are complete and accurate.
4. Collaborate With Accredited Testing Providers
If your company lacks in-house expertise, partner with accredited providers like Terradyne. With years of experience and reliability in construction materials testing, we ensure accurate results for your projects are delivered on time.
5. Schedule Regular Reviews & Quality Audits
Continuous improvement is key. Set regular milestones for internal reviews and involve third-party auditors to assess your process integrity. Keeping quality at the forefront builds resilience against costly errors.
Terradyne: Prioritizing Quality for Long-Term Success
Construction materials testing isn’t just a regulatory obligation; it’s a fundamental process for delivering safe, high-quality projects that stand the test of time. By understanding common mistakes and how to avoid them, construction professionals can safeguard their projects and avoid disruption.
At Terradyne, we pride ourselves on helping construction professionals achieve precisely that. Our state-of-the-art testing services and team of expert geotechnical engineers are ready to help you streamline testing operations and raise quality standards.
Contact us for more information on how our team can help you take your project from concept to vertical!